Duplex stainless steels: what does it mean to be super?
Duplex stainless steels are steels with a dual ferritic–austenitic microstructure, both considered stainless as the chromium content of each phase is well above 12 wt%.[ref]Krauss, G. in Steels: Processing, Structure, and Performance Ch. 23 “Stainless steels,” 495-534 (ASTM International, 2005).Buy at Amazon[/ref]
To be considered “super” the alloy should have a pitting resistance equivalent (PRE) above a value of 40.[ref]ISO 21457:2010, “Petroleum, petrochemical and natural gas industries — Materials selection and corrosion control for oil and gas production systems” (Geneva, Switzerland: International Organization for Standardization, 2010).[/ref],[ref]Skar, J. I. & Olsen, S., “Development of the NORSOK M-001 and ISO 21457 Standards – Basis for Defining Materials Application Limits,” CORROSION/16, paper no. 7433 (Vancouver, British Columbia, Canada: NACE International, 6-10 March, 2016).
[/ref]
What is the PRE of an alloy you ask?
Well, it is complicated. For now, let us just say that, early on, researchers tried to correlate the localized corrosion resistance of stainless steels and composition. Lorenz and Médaward where the first ones to propose the so-called wirksumme,[ref]Lorenz, V. K. & Médawar, G. Über das Korrosionsverhalten austenitischer Chrom-Nickel-(Molybdän-) Stähle mit und ohne Stickstoffzusatz unter besonderer Berücksichtigung ihrer Beanspruchbarkeit in chloridhaltigen Lösungen. Thyssenforschung 1, 97-108 (1969).
[/ref] an index that related the chromium and molybdenum content of stainless steels to the pitting corrosion resistance of the material. Since their original work, a plethora of “equivalent sums” or indices has been proposed. We will discuss the history of the PRE concept in more detail later, but if you are interested, I strongly recommend reading the article by Jargelius-Pettersson,[ref]Jargelius-Pettersson, R.F.A. Application of the pitting resistance equivalent concept to some highly alloyed austenitic stainless steels. Corrosion 54, 162-168, doi:10.5006/1.3284840 (1998).
[/ref] which has an excellent review of the various formulae.
Today, most international standards define a PRE expression of the generic form:
$$ PRE = Cr + a \cdot (Mo + b \cdot W) + c \cdot N \tag{1} \label{eq:1}$$
where the concentrations in \eqref{eq:1} are written in wt% and the multipliers \(a\), \(b\), and \(c\) may take different values.
Whereas ISO, API, ASTM, and NACE standards define PRE as:
$$ PRE_{N, W} = Cr + 3.3 \cdot (Mo + 0.5 \cdot W) + 16 \cdot N \tag{2} \label{eq:2}$$
NORSOK M–001 does not allow the inclusion of tungsten in the formula. Thus, NORSOK PRE definition is:[ref]NORSOK M-001, “Materials selection” (Lysaker, Norway: Standards Norway, 2014).
[/ref]
$$ PRE_{N} = Cr + 3.3 \cdot Mo + 16 \cdot N \tag{3} \label{eq:3}$$
But why?
Does tungsten influence localized corrosion resistance?
Regardless of the PRE definition, in the oil and gas industry, all standards treat the various super duplex stainless steels (SDSS) as being equivalent or interchangeable.
Tungsten, which translates from the Swedish tung sten as “heavy rock,” has been shown to improve pitting corrosion resistance of stainless steels.[ref]Sedriks, A. J. Plenary Lecture—1986: Effects of Alloy Composition and Microstructure on the Passivity of Stainless-Steels. Corrosion 42, 376-389, doi: 10.5006/1.3584918 (1986).[/ref] Some researchers claim that, when normalized to its atomic weight, tungsten had a positive effect comparable to that of molybdenum. Hence, one of the original PRE formulae did not have the 0.5 multiplier in front of W. However, the effect of tungsten on crevice corrosion resistance of commercial SDSS has not been independently quantified until now.
Together with my colleague Professor Roy Johnsen and our former students Eirik Haugan, Monika Næss, and our Ph.D. student Cristian Torres Rodriguez, we have recently published a comprehensive investigation comparing the influence of tungsten on pitting and crevice corrosion of commercial SDSS. We studied UNS S32750 and UNS S39274, an SDSS with about 2 wt% W. The manuscript is OpenAccess so you can download it for free from the CORROSION Journal website or by clicking on the image below.
Spoiler alert
In the solution annealed condition, i.e., as used in service and free from deleterious phases, tungsten dramatically improved crevice corrosion resistance. Thus, we believe that standards like ISO 21457 and NORSOK M–001 should revisit their approach towards SDSS. The localized corrosion resistance of UNS S39274 was similar to that of UNS S31254, an austenitic stainless steel with 6 wt% Mo and a \(PRE_{N}\) of 43.
Abstract
The oil and gas industry regularly uses Type 25Cr super duplex stainless steels for components exposed to seawater and hydrocarbon environments in topside facilities, downhole, and subsea equipment. Much debate still exists concerning the effect of tungsten on pitting and crevice corrosion resistance, particularly in standardization committees. Whereas some researchers claim that tungsten has a strong synergistic effect with molybdenum when added above a certain threshold value, others argue that tungsten additions at the expense of molybdenum could lower corrosion resistance.
The objective of this investigation was to examine the effect of tungsten on localized corrosion of two super duplex stainless steels: a low-W (mod. UNS S32750) and a high-W (UNS S39274) grade. Both crevice-free and creviced samples were studied. Tests were conducted in 3.5 wt% NaCl or natural seawater with temperatures ranging from 20 to 95°C. Various independent methodologies including cyclic potentiodynamic polarization, electrochemical critical pitting temperature testing according to ASTM G–150, and long-term open circuit potential exposure in natural seawater were employed.
Results showed that, in the solution annealed condition, tungsten additions to super duplex stainless steels had a marked positive effect on pitting and crevice corrosion resistance, increasing critical crevice temperatures by as much as 30°C. These findings suggested that tungsten-containing SDSS had a corrosion resistance on a par with super austenitic stainless steel grades containing 6 wt% molybdenum. A new parametric definition of the Pitting Resistant Equivalent is proposed to reflect the alloy’s localized corrosion resistance and to support standardization efforts in the materials oil and gas community.
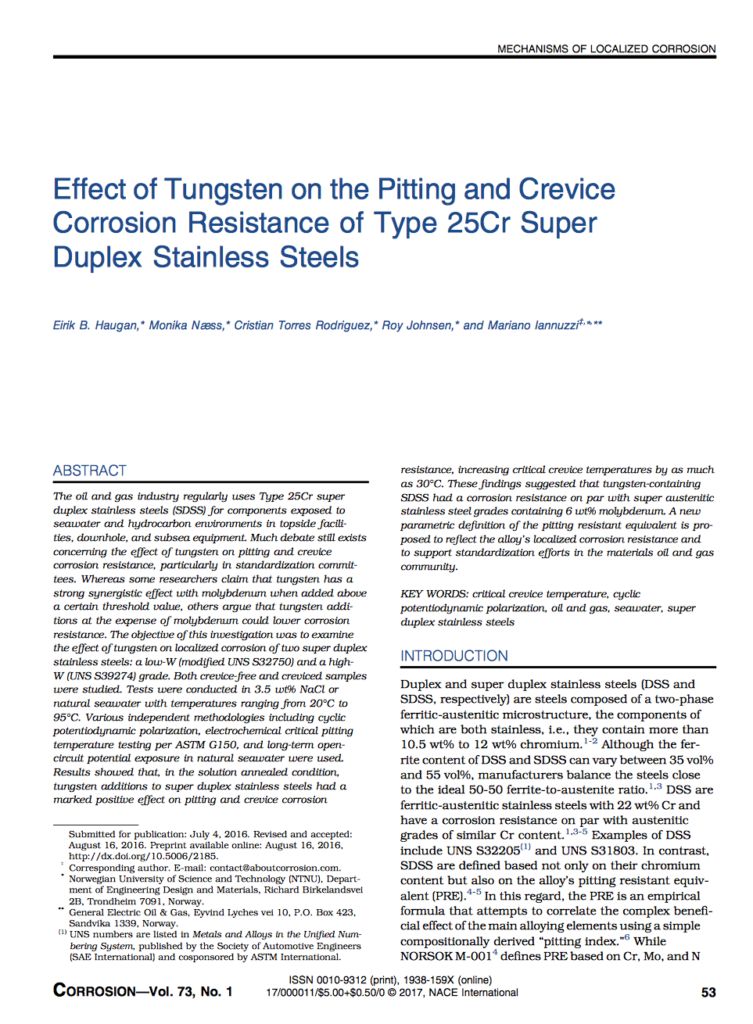
[altmetric doi=”10.5006/2185″ type=”donut” condensed=”true” data-hide-no-mentions=”false” popover=”right” details=”right”]
Citation
Haugan, E. B., Næss, M., Rodriguez, C. T., Johnsen, R. & Iannuzzi, M. “Effect of Tungsten on the Pitting and Crevice Corrosion Resistance of Type 25Cr Super Duplex Stainless Steels.” Corrosion 73, 53–67, doi: 10.5006/2185 (2017).
Acknowledgements
We thank Atle H. Qvale (GE O&G), Alexander Fjeldy (GE O&G), Leif Brattås (GE O&G), Anders Wiktorsson (GE O&G), Mariano A. Kappes, and Ricardo M. Carranza (Instituto Sabato, Buenos Aires, Argentina) for their guidance, support, and technical discussions.
We also thank Mitsuru Yoshizawa, Nippon Steel & Sumitomo Metal Corp., for providing samples for testing as well as General Electric (Oil & Gas) and the Norwegian University of Science and Technology for sponsoring this work.